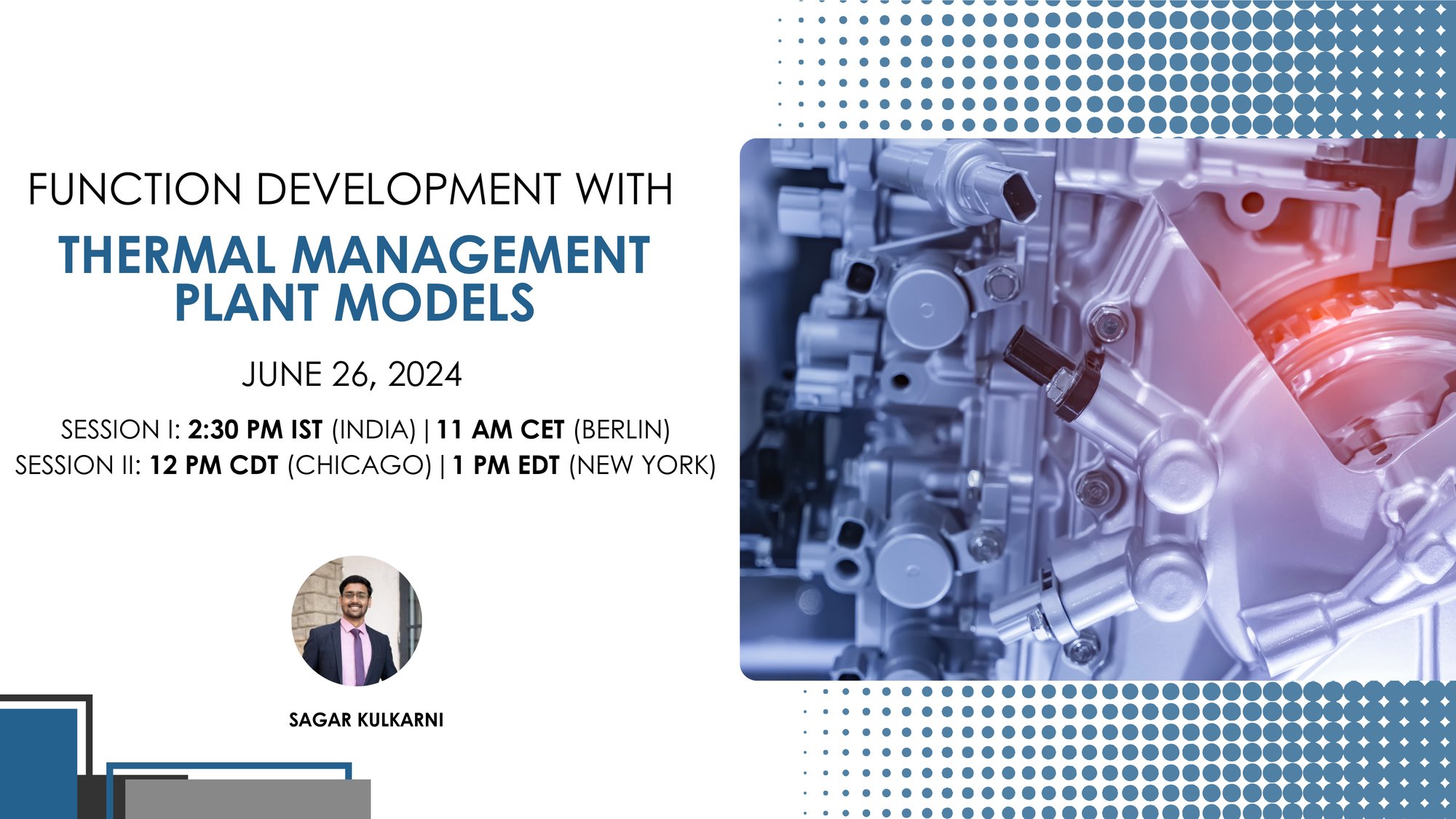
-
Learn how to streamline the design process of thermal management systems for electric vehicles, optimizing their efficiency and range.
-
Leverage virtual testing and HiL simulations to validate thermal management solutions without physical hardware.
-
Discover how virtualizing vehicle design and testing streamlines decision-making, cuts costs, and speeds up development.
Abstract
The shift to electric vehicles (xEVs) poses complex thermal-management challenges for automotive engineers. These electrified vehicles require intricate systems to control temperatures and optimize range. To address these challenges, the industry is turning to virtual testing and validation through Hardware in the Loop (HiL) simulations.
The demand for electrical energy to condition the battery and cabin, as well as for propulsion, means that a holistic approach to thermal management simulation is needed today to retain the most efficiency of the systems.
For this reason, the industry is shifting toward complete virtualization of vehicle design and then validation through virtual testing, including Software and Hardware in the Loop (HiL) simulations. This approach allows for early validation of new technologies without the need for physical hardware, reducing testing costs, development cycle times, and enhancing decision-making throughout the development of the powertrain.
The study conducted in this paper investigates methods aimed at streamlining complex thermal management models of Battery Electric Vehicles (BEVs). A high-fidelity model of a BEV is used, featuring detailed thermal representations of components and a number of cooling, chiller, and AC circuits. The focus is on reducing runtime while finding the right compromise with accuracy and predictivity.
From an initial high fidelity model that runs significantly slower than real-time, multiple guided approaches were applied to facilitate a robust reduced order modeling approach. First by transitioning from 3D to 1D thermal modeling for the motor and coolant plate and then simplifying flow systems; the runtime is reduced to faster than real-time. This fast-running model maintains accuracy while making it suitable for HiL testing.
Finally, by implementing a unique parallel threading approach and splitting the integrated model into parallel sub-models running on multiple cores, real-time execution on HiL systems is achieved. This approach enables efficient testing and validation of thermal management systems without compromising accuracy.
In conclusion, this study highlights the successful development of a fast-running model for complete vehicle thermal management. It simplifies complex models, accelerates runtime, and enables HiL testing, offering a cost-effective and accurate approach for xEV development.
Topics include:
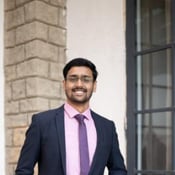
Sagar Kulkarni | Presenter
Application Engineer | Thermal Fluid Systems at Gamma Technologies